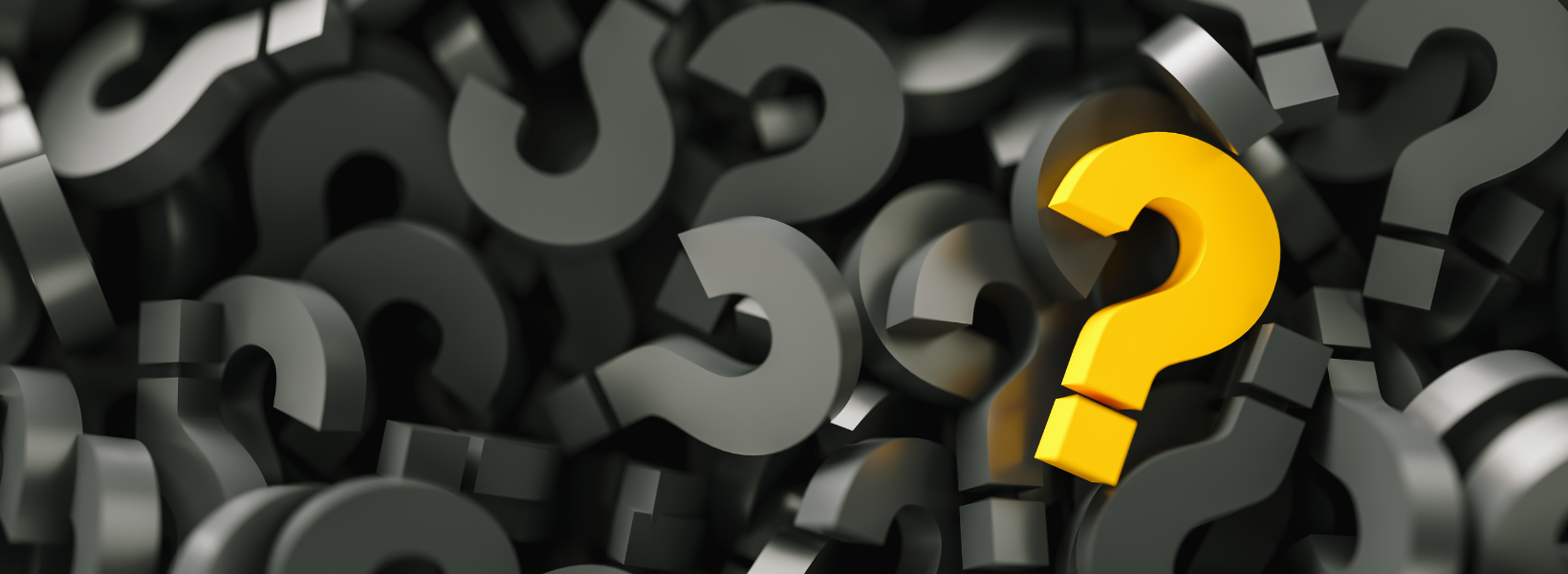
Frequently Asked Questions
WHAT IS 6D ROAD SCANNING?
The LiDAR is mounted on top of a regular vehicle and digitizes the road surface, collecting a total of six types of data outputs (6D) of the pavement surface:
– 3D geometry model (point cloud)
– 3D model of the reflectivity (point cloud with one extra dimension) and
– 2D camera images.
All data collected is annotated with detailed RTK GNSS data. This short-range LiDAR measures pavement digitally with a resolution down to 5 mm in both driving and lateral directions. The XenomatiX’ 6D Road Scanning system provides road condition measures based on objectively measured and certified road characteristics, allowing for virtual analysis of road conditions and identification of causes and repair solutions.
ARE XENOMATIX’ SENSORS CERTIFIED SYSTEMS?
All XenomatiX LiDARs are Class 1 certified for eye safety. Additionally, the XenoTrack Road LiDAR system is certified Class 1 in accuracy, repeatability and efficiency for IRI, Rutting and raw profiles (IRI: ASTM 950 – E1926 – AASHTO 56 – Rutting: ASTM E1703 – EN 13036-8) by both NCAT and ICART.
WHAT IS THE MAIN DIFFERENCE BETWEEN XENOTRACK AND OTHER LASER SCANNERS?
The XenoTrack Road LiDAR is designed to measure road surfaces with millimeter precision. Each frame captures a full 4m wide x 2m long area of the road surface in a global shutter at 40 Hz. Consecutive measurements overlap, enabling construction of an optimized digital model of the road. Unlike other systems, the XenoTrack measures a surface (not just a line), so its algorithm handles autonomously corrections for car movements (roll, pitch, and yaw). With overlapping surface data, any small car movement is calculated and corrected without needing input from an IMU or a dual laser setup. In other systems, movement corrections can accumulate errors and cause inaccuracies due to reliance on acceleration measurements or single-point laser measurements.
AT WHAT SPEED CAN THE XENOTRACK ROAD LIDAR COLLECT DATA, AND CAN IT STOP AND RESTART DURING DATA COLLECTION?
XenoTrack can collect data at speeds ranging from 0 km/h to 90 km/h, effectively avoiding motion blur. It also supports start-and-stop manoeuvres, enabling it to stop and restart at stop signs or traffic lights during data collection. This capability is achieved through the overlap of individual surface-covering point clouds and the DMU.
IS THERE A YEARLY LICENSE FEE?
No, there is no yearly license fee required. Customers purchase and own the software outright, with an optional maintenance contract available for free upgrades.
WHAT IS A DIGITAL TWIN?
The Digital Twin is an innovative tool for saving both cost and time, helping prioritize choices in road inspection, maintenance, and road safety. Digital Twins are increasingly popular with national and local governments. With a 3D, 4D, or 6D digital copy of the road network, users can inspect roads virtually, monitoring deterioration in safety and comfort over time. By collecting digital copies of multiple assets (e.g., roads, bike paths, sewers), local authorities can gain valuable insights for planning necessary work and saving on budgets.
WHAT DATA OUTPUT DOES XENOTRACK PROVIDE?
The XenoTrack Road LiDAR system generates several data outputs, including:
– 3D geometrical model of the pavement surface;
– 3D intensity model of the pavement surface;
– Automatically calculated International Roughness Index (IRI) (ASTM 950, E1926, AASHTO 56)
– Automatically calculated Rutting index (ASTM E1703, EN 13036-8)
– Automatically calculated Mean Profile Depth (MPD) (ASTM E1845-15, ISO 13479-1)
– Cracks and other surface features
HOW DO YOU DEFINE GLOBAL ACCURACY?
Global accuracy refers to 3D geometry that is referenced to the absolute world coordinate system. All measured and analyzed data is georeferenced and ready for import into any GIS system.
WHAT IS A TRUE SOLID-STATE LIDAR?
Traditional LiDAR systems rely on rotating lasers to scan surroundings. This use of moving parts makes them sensitive to factors like rough terrain or heavy rain and imposes size limitations. Smaller sizes require high manufacturing precision, raising costs. In contrast, a true solid-state LiDAR has no moving or scanning parts, making it more robust and scalable. Solid-state LiDARs are made with silicon chip technology, which enhances resilience to vibrations and allows for compact sizes. Many lidars pretend to be solid-state but use MEMS technology (Micro Electro Mechanical System), by definition not solid state; therefore true solid-state.